How to make a box that utilizes all three functions of a Snapmaker 3-in-1 3D printer?
3D-print, Laser-cut, CNC-carve, do it all in one printer!
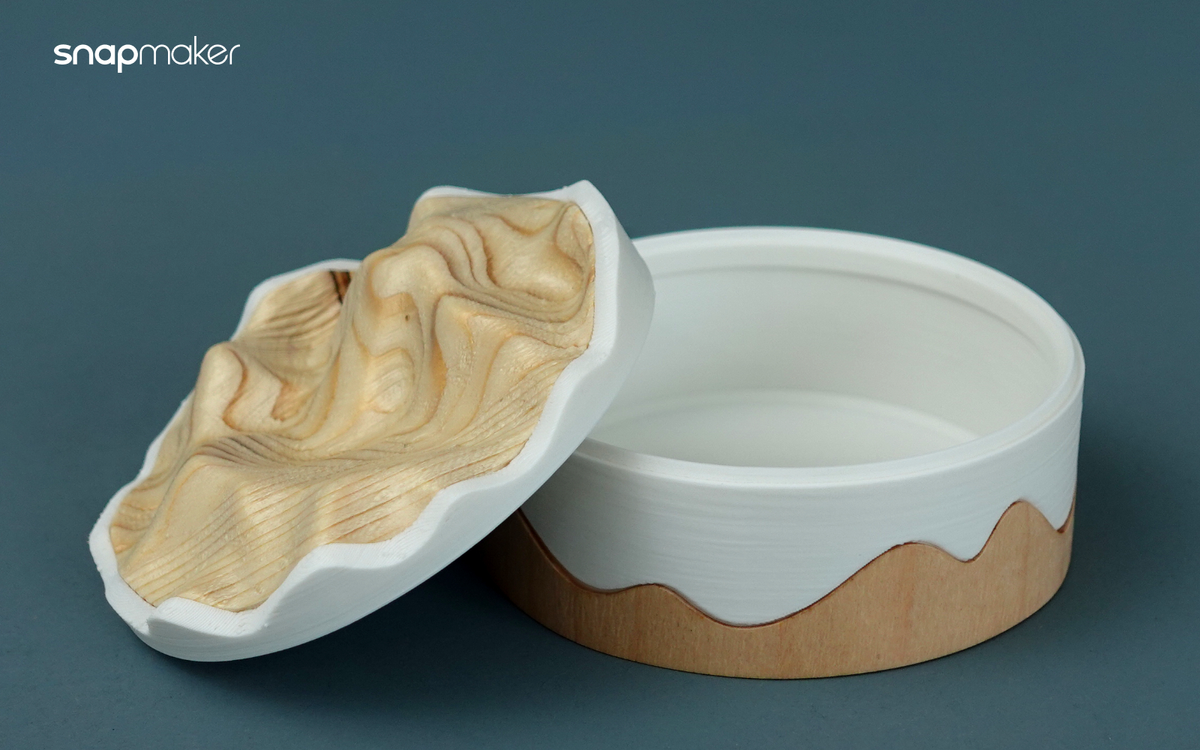
We often get asked this question by users. Where can I find a project that uses all three functions (3D printing, Laser, and CNC) of a Snapmaker 3-in-1 3D printer? We are here to help! Today, we will share a tutorial by the designer gazzaladra, featuring the making of a beautiful 3-in-1 box (size of the box: 92 x 92 x 48 mm) named “Hills.” gazzaladra is a designer from Germany, who designs useful and enjoyable products for household use. Follow the detailed steps below, and make your own!
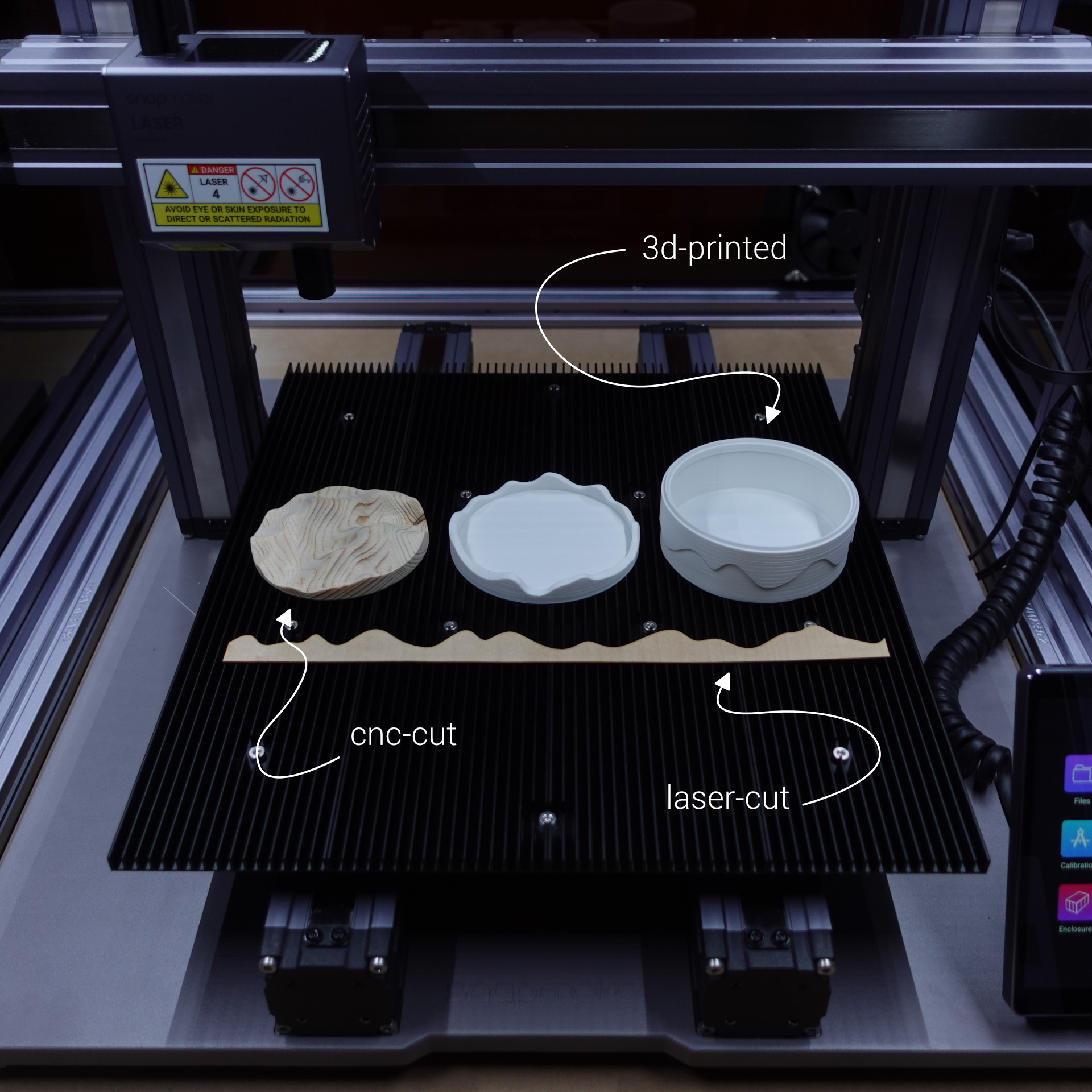
Step 1 Prepare tools and materials
Material:
- 3D printing filament (preferably White PLA)
- 16mm thick wood
- 1mm thick wood veneer
- A glue that can bind PLA and wood together
Tools:
- A 3-in-1 3D printer like Snapmaker 2.0 A250T/A350T, Snapmaker Artisan (*Please note that users should always operate the 10W Laser Module with the Snapmaker 2.0 Enclosure covered and wear laser safety goggles.)
- Snapmaker Luban (software installed)
- Design files of the Box (download for personal use only)
Step 2 3D-Print the body and the lid
To begin this project, we will need to print the body and lid of this box. It is an easy print, and you can use your default settings to slice the STL or use the pre-sliced g-code prepared by gazzaladra.

Estimated time: 5 hours
Material: 3D printing filament (preferably White PLA)
Material usage: 50g
Support: none
Nozzle size: 0.4 mm
Line width: 0.4 mm
Layer height 0.2 mm
Outer walls: 3
Infill: 15%
Build plate adhesion type: none
Files:
Box_body.stl
Box_lid.stl
Box_body+lid.gcode
Step 3 CNC-cut the wooden lid
The second thing we are going to manufacture is the wooden lid.
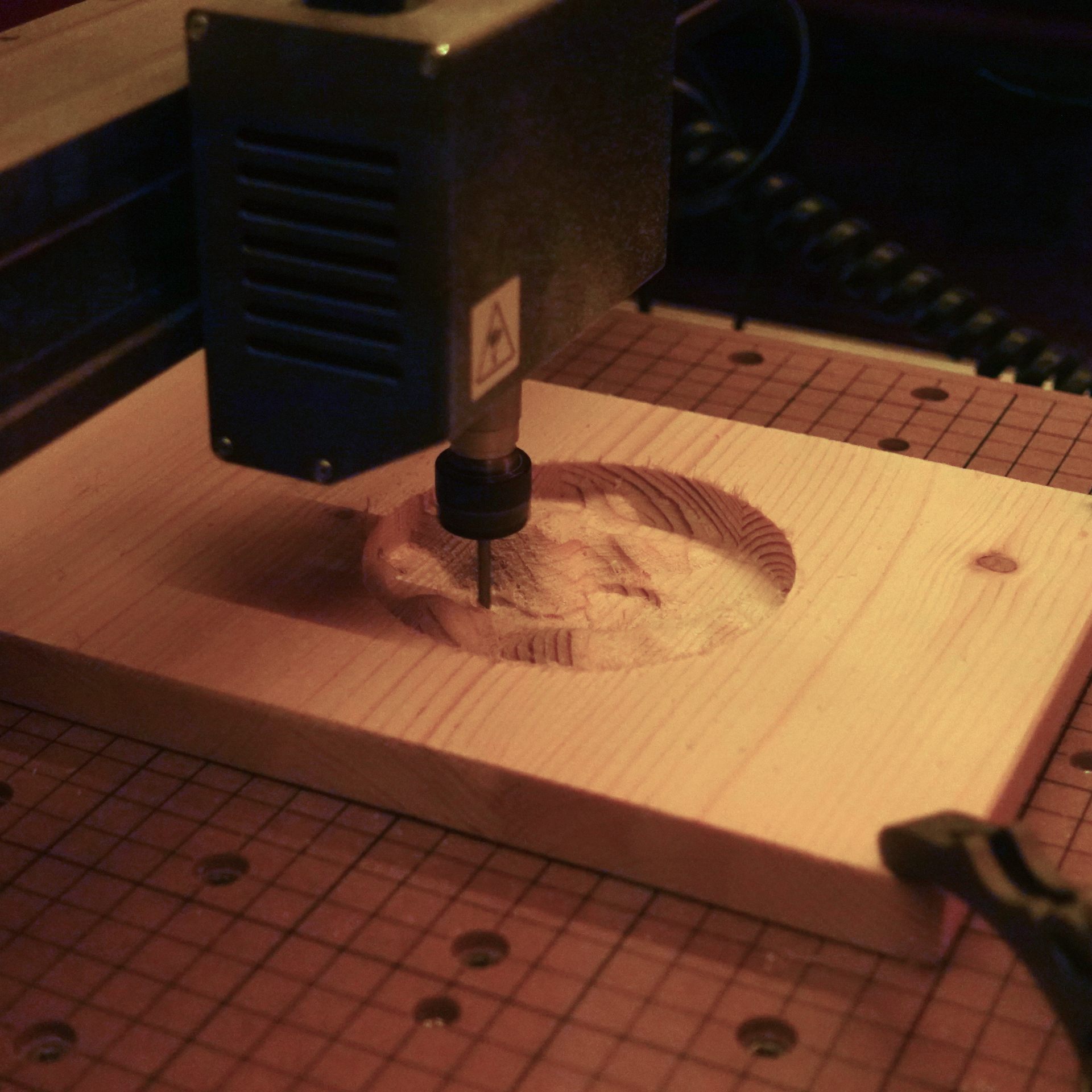
Estimated time: 2 hours
Material: 16mm thick wood. The CNC code is optimized for softwood. If you want to use the hardwood, we recommend processing the STL file according to the properties of your wood. The inlay is 84mm in diameter. You need some extra material on the sides of the workpiece to clamp it down. I, therefore, recommend a piece that is 150x150mm, which is able to safely process it.
Step-by-step:
- Either use the existing CNC file or process the STL file yourself.
- Install the 3.175 Ball End Mill.
- Mark the center of your piece of wood.
- Mount the workpiece on the MDF wasteboard.
- Calibrate the starting point.
- Run the boundaries to check for possible collision with the clamps
- Start the code. Don’t forget to put on your safety goggles!
- Stay with the machine and stop occasionally to remove the wood shavings with a vacuum cleaner.
- Once it is finished the inlay should detach from the wooden board quite easily. The edge may require some sanding.
- Optional: You can use oil or varnish of your choice to give it a nice finish.
Files:
Box_inlay.stl
Box_inlay.cnc
Step 4 Laser-cut the rim
Now we will make the last piece–the laser-cut rim!
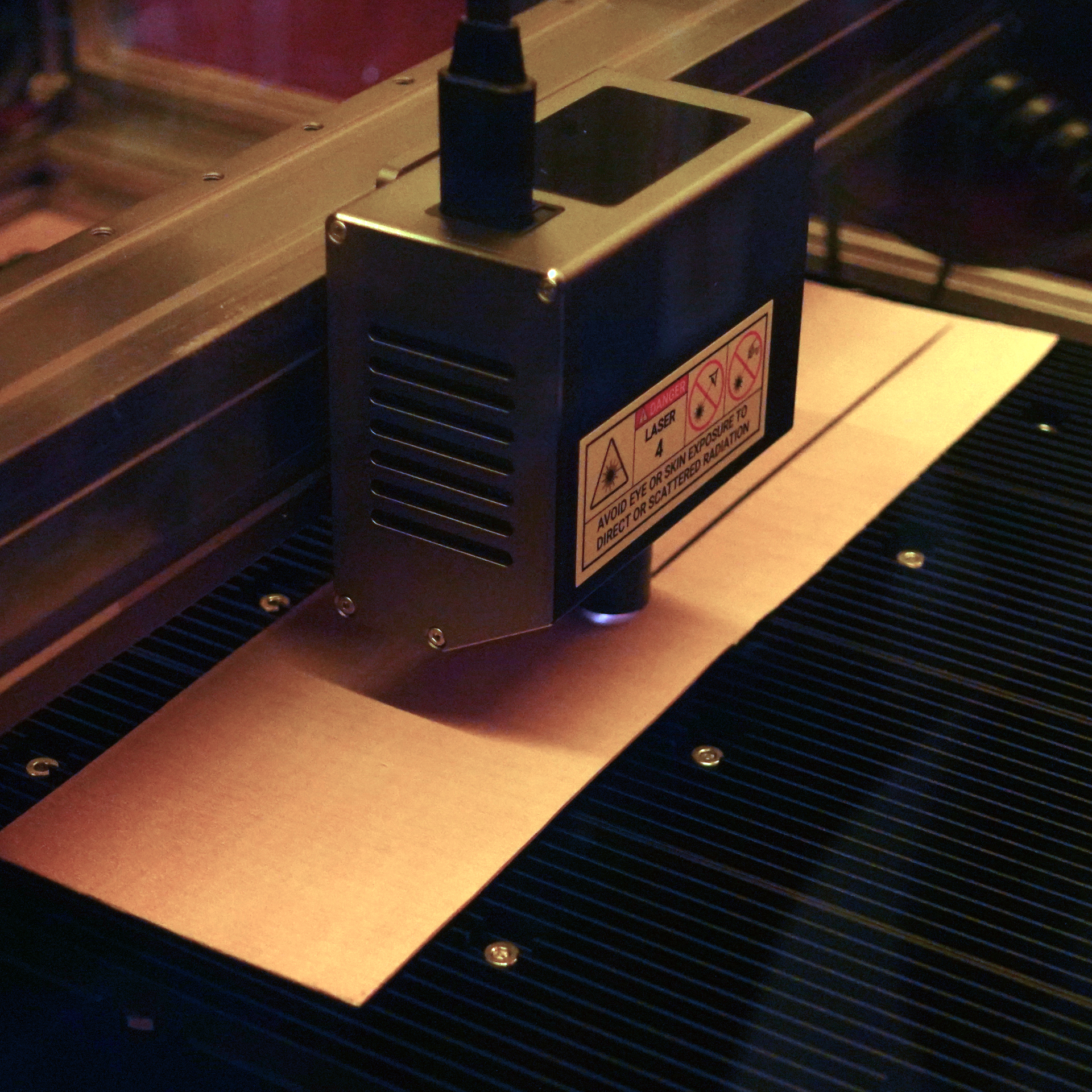
Estimated time: 5 minutes
Material requirements: 1mm thick wood veneer. The final size of the piece is about 290 × 22mm. I recommend cutting it against the wood direction (check the image). You need some extra material on the sides of the workpiece to fix it in place. I, therefore, recommend a piece that is 300 × 40 mm big to be able to safely process it.
Work speed: 140mm/min (for the 1600mW Laser Module)
Jog speed: 3000mm/min (for the 1600mW Laser Module)
Power: 100% (for the 1600mW Laser Module)
Number of passes: 1
Step-by-step:
- Import the DXF file into Luban.
- To process it on Snapmaker 2.0 A250T, you need to rotate it by 45 degrees to fit the build size.
- Create your toolpath with the settings mentioned above or create your own for the 10W Laser Module and export it to your machine.
- Cut the right-sized piece from your veneer with a sharp cutter.
- Configure the focal length.
- Attach the veneer to the build surface with either double-sided tape or the silicon knobs.
- Configure the center and run the boundaries
- Start the code. Don’t forget to put on your safety goggles! Once it is finished, remove the piece carefully
- Optional: You can carefully sand the black laser traces for a nicer look.
Files:
Box_rim.dxf
Step 5 Assembly
Once you finish manufacturing all pieces, you can continue to assemble them.
Step-by-step:
1. Get the glue that can bind PLA and wood together (regular super glue does a great job)
2. Insert the inlay into the lid. It should fit with a little friction. If it is loose, use a little glue.

3. Glue the rim to the base. Then, a beautiful box with a pattern of undulating hills is done!
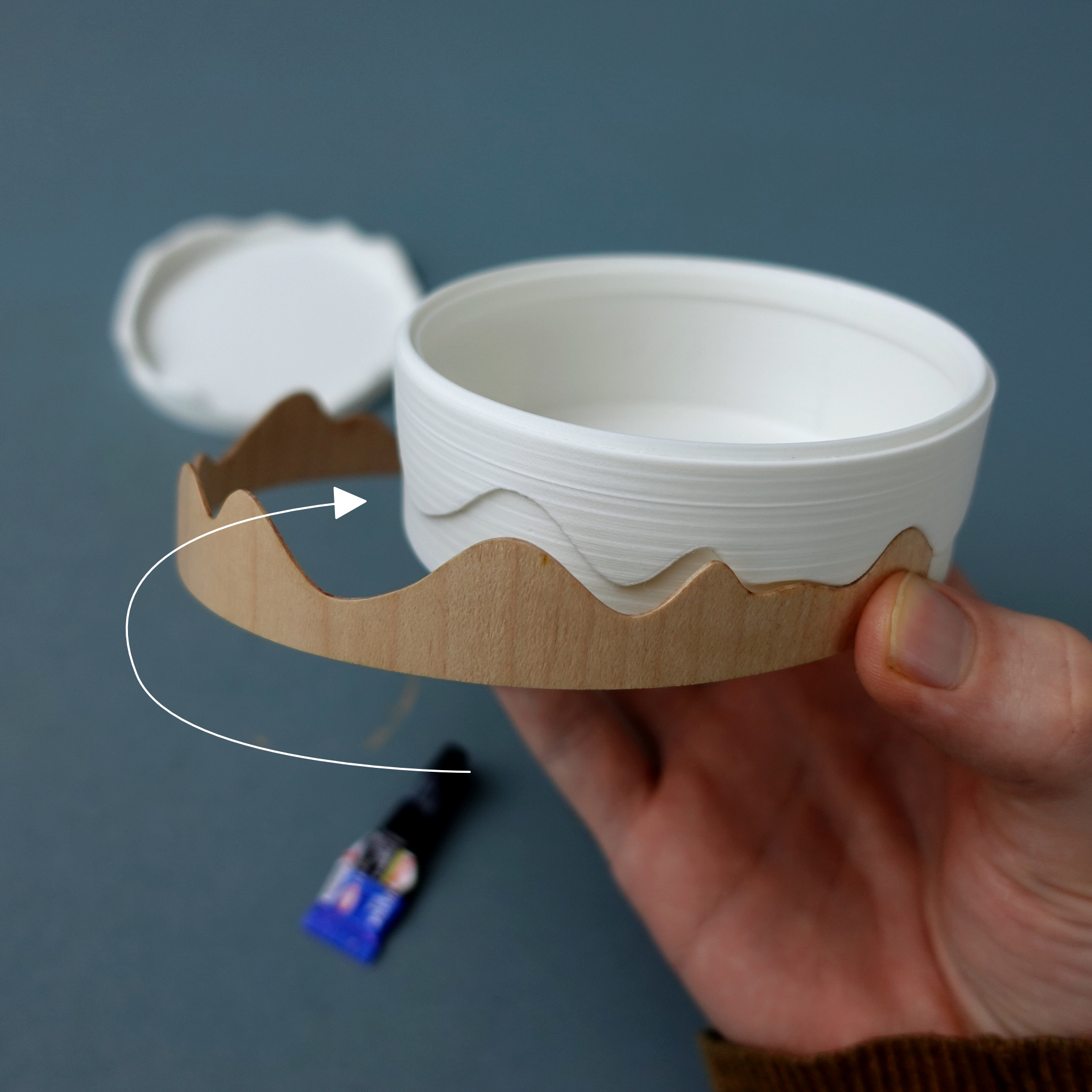
4. Post pictures of your box on social media and tag gazzaladra and Snapmaker!
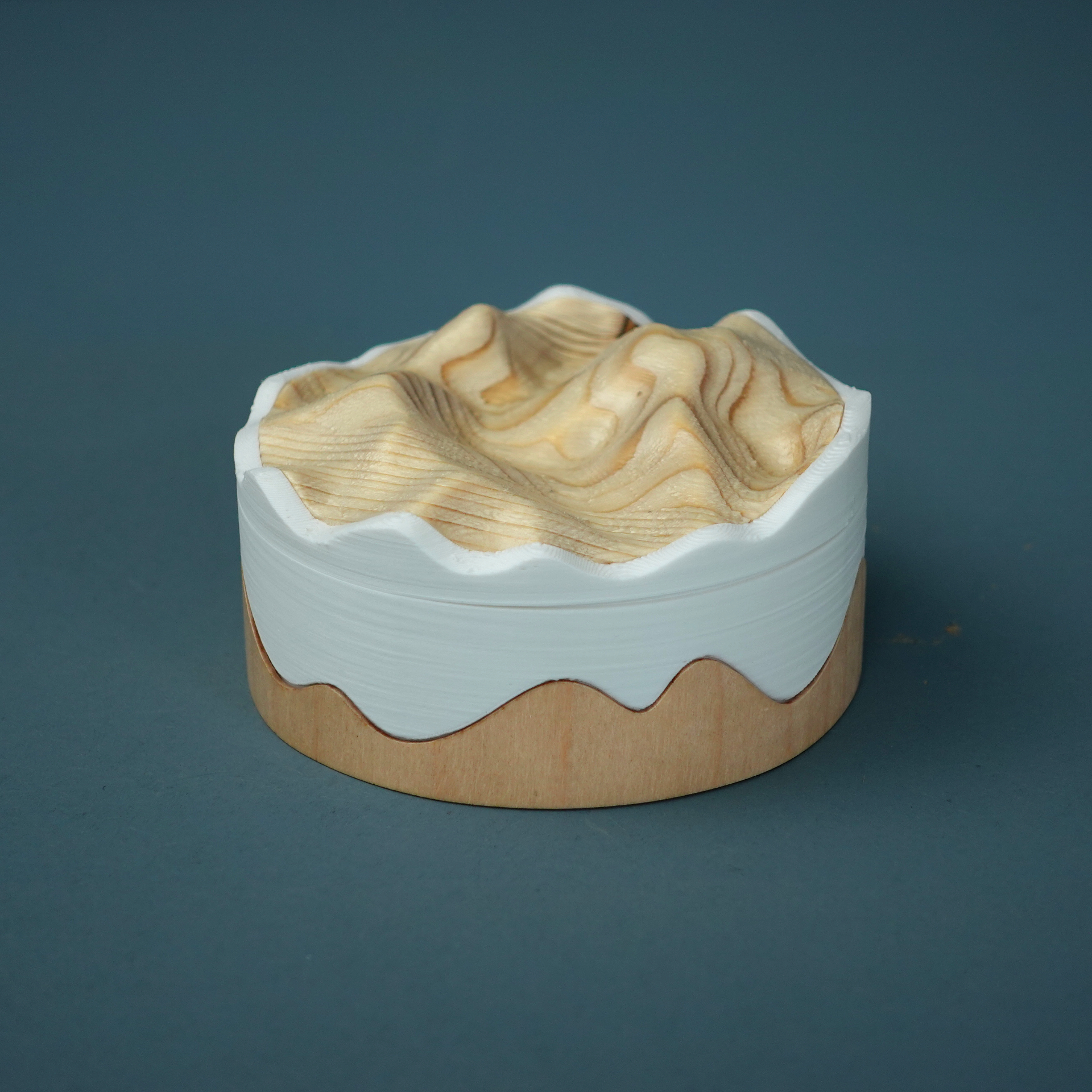
If you are looking for more designs by gazzaladra, you can check out gazzaladra’s profiles on Cults.