Can You 3D Print Rubber? A Guide to Flexible 3D Printer Filament
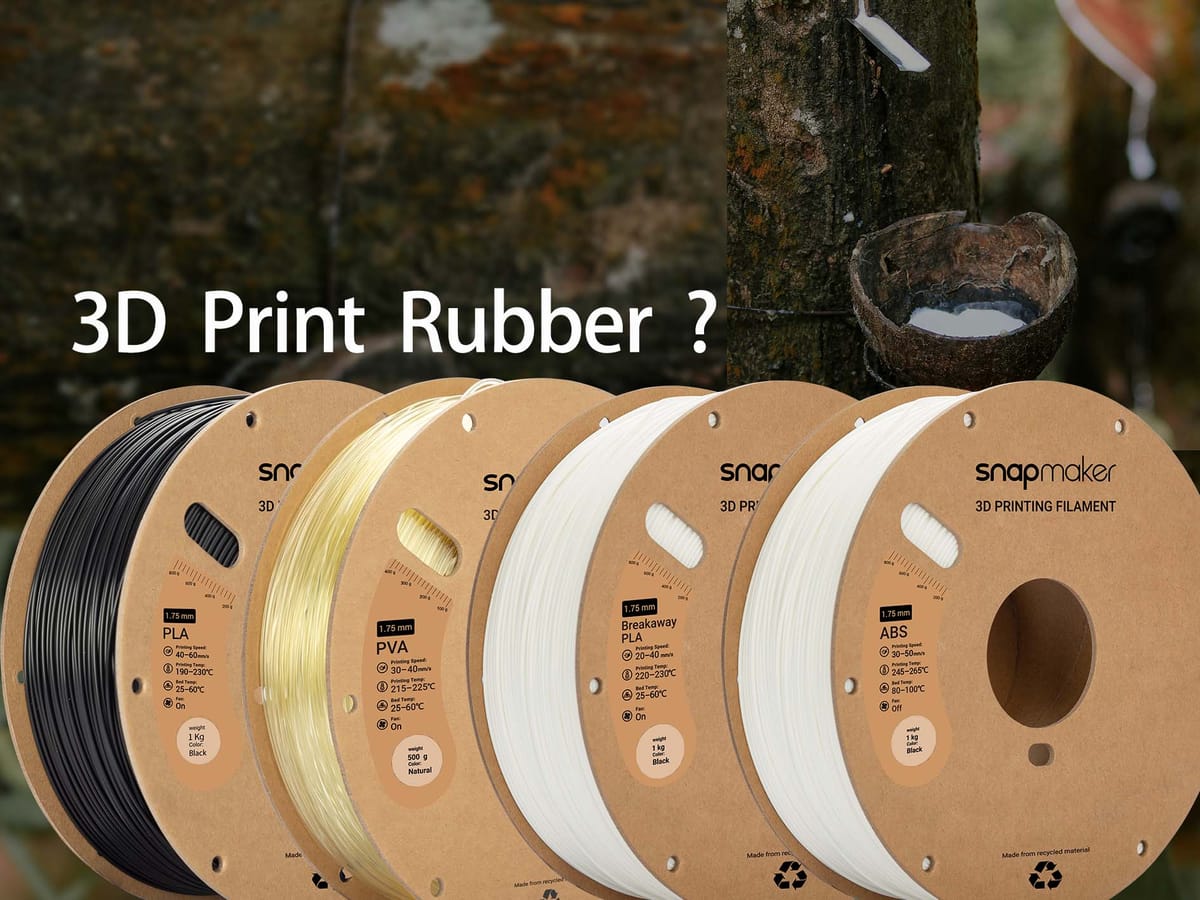
Can you 3D print rubber? No. Wait a minute; that's not the end of the story! Rubber itself can't be 3D printed; you can print objects as if they were made of rubber using flexible 3D filaments. This blog addresses why rubber cannot be 3D printed while highlighting everything you need to know about flexible 3D filaments.
Can Rubber Be 3D Printed? The Yes and No Answer
Do you know if rubber can be 3D printed? In short, no 3D printer technology is currently available for printing rubber. We wouldn't bet on technology that will be able to handle rubber anytime soon. The reason lies in rubber—specifically, the difference between thermosetting and thermoplastic materials.
Rubber is a thermosetting material. Once heated, it cures and cannot be returned to its fluid state without decomposing, unlike thermoplastics like PLA or ABS. It also releases toxic fumes in the process.
This makes it unsuitable for traditional 3D printing processes, such as additive manufacturing, where materials are re-melted and shaped layer by layer. Rubber is usually produced by injection molding, a process where the raw material is poured into the mold and allowed to set, and it is very far from 3D printing.
The good news, however, does exist! While actual rubber cannot be 3D printed, you can get a similar feel from other materials with the flexible feel you want. Silicone 3D printing has been impressive lately, and if you want a custom part with rubber-like properties, you can print a mold and cast it with silicone.
Another route is using flexible 3D printer filament like TPU, which gives you the same elastic qualities without ever printing rubber. While the answer is no for rubber, flexible 3D printing filaments give a hearty yes to your need for stretchable, soft models.
Understanding Flexible 3D Printer Filament
What Are Flexible Filaments
Thermoplastic elastomers, or TPE, are flexible filaments that blend the properties of hard plastic and rubber. As expected, this makes for a highly stretchy, easily bent elastomeric material. However, there are several types of TPE filaments, and the most common among 3D printing filaments is thermoplastic polyurethane (TPU). TPU features rubber-like properties, such as flexibility and resistance to chemicals. TPU can be printed using common techniques such as fused deposition modeling (FDM).
- Elasticity
TPU is an elastomer resembling rubber but does not have fundamental rubber 3D filament properties. Its ability to bend and compress is also shock-resistant, and it contains desirable attributes like vibration dampening. It can easily be modified by altering its composition. TPU material ranges from very hard to quite flexible.
- Durability
Another reason TPU is suitable for some consumer applications is that it does not suffer from surface damage. TPU is strong and less prone to wear and tear. Even high stress does not tend to deform prints made using TPU.
- Chemical resistance
As if all that wasn't enough, TPU is also a good repeller of chemicals, especially oil and grease. Polyester TPUs are the best for resisting oils, whereas polyether TPUs are used in moisture environments where the hygroscopic properties of the material must be minimized.
- Shore hardness scale
The softness or hardness of flexible filaments is measured on the Shore hardness scale, with lower values being softer and more flexible.
Material hardness has three different Shore scales:
-
- Shore 00: For very soft materials such as gels and rubber.
- Shore A: It is used for flexible rubber filament and rigid plastics.
- Shore D: For brittle plastics and hard rubber
Shore hardness is measured by a durometer, which measures the hardness of a material. A durometer test applies to soft and flexible plastics. There is also a Rockwell test for hard plastics such as polycarbonate.
Knowing the shore hardness of the material you’re printing with is helpful if, for example, you’re printing a mold. You’ll know that a softer material with a shore hardness of around 30-40A will produce a flexible mold from which you can easily extract things. If the mold is too rigid, then the removal of the part can lead to the part breaking or cracking.
Common Types of Flexible Filaments
- TPU (Thermoplastic Polyurethane)
- TPE (Thermoplastic Elastomer)
- TPC (Thermoplastic Copolyester)
Pro tips: Essentially, TPE encompasses a range of materials, while TPU is a specific type within that group. In 3D printing, filament manufacturers often present TPU and TPE as distinct options, with TPU being the harder, more durable choice, and TPE typically referring to softer, more flexible materials.
Best Practices for Printing with Flexible Filaments
Printer Setup
1. Direct drive extruders vs. Bowden setups
Even though some partially flexible filaments can work perfectly well with Bowden extruders, most fully flexible filaments are best printed using a direct drive extruder. This means that the drive gear should be positioned as close to the melt zone of the hot end as possible so that proper feeding of the filament into the nozzle occurs.
Furthermore, the filament's path to reach the melt zone should be held within tight tolerances so that the filament does not kink or coil inside. For these reasons, printing flexible filaments is usually much easier with a direct drive extruder than a Bowden extruder. If you're unsure whether your 3D printer will work, you may want to call the manufacturer to ask if the extruder is certified for printing flexible filaments.
2. Nozzle considerations
A larger nozzle (around 0.4mm or greater) can help ensure smooth filament flow and reduce the risk of clogging.
Slicer Settings
1. Print speed
Flexible filaments usually print best at low and steady print rates. Due to the elastic nature of the material, it can sometimes be nearly impossible to control sudden changes in print speed. Higher print speeds will cause the filament to be squeezed, and you almost certainly will jam. Slow and steady is best. Usually, 20-40 mm/s is the ideal range. With High Flow TPU95 (TPU95-HF), a specialty filament, you can print at higher speeds: 80-100 mm/s.
2. Temperature
- Printing temperature: 200-230˚C
- Heated bed temperature: 25-60˚C
The bed temperature is usually not as much of an issue when printing flexible filaments, as flexible filaments tend to be very sticky. In addition, flexible filament manufacturers may recommend a cooling fan speed of about 50%, particularly when printing small or delicate details.
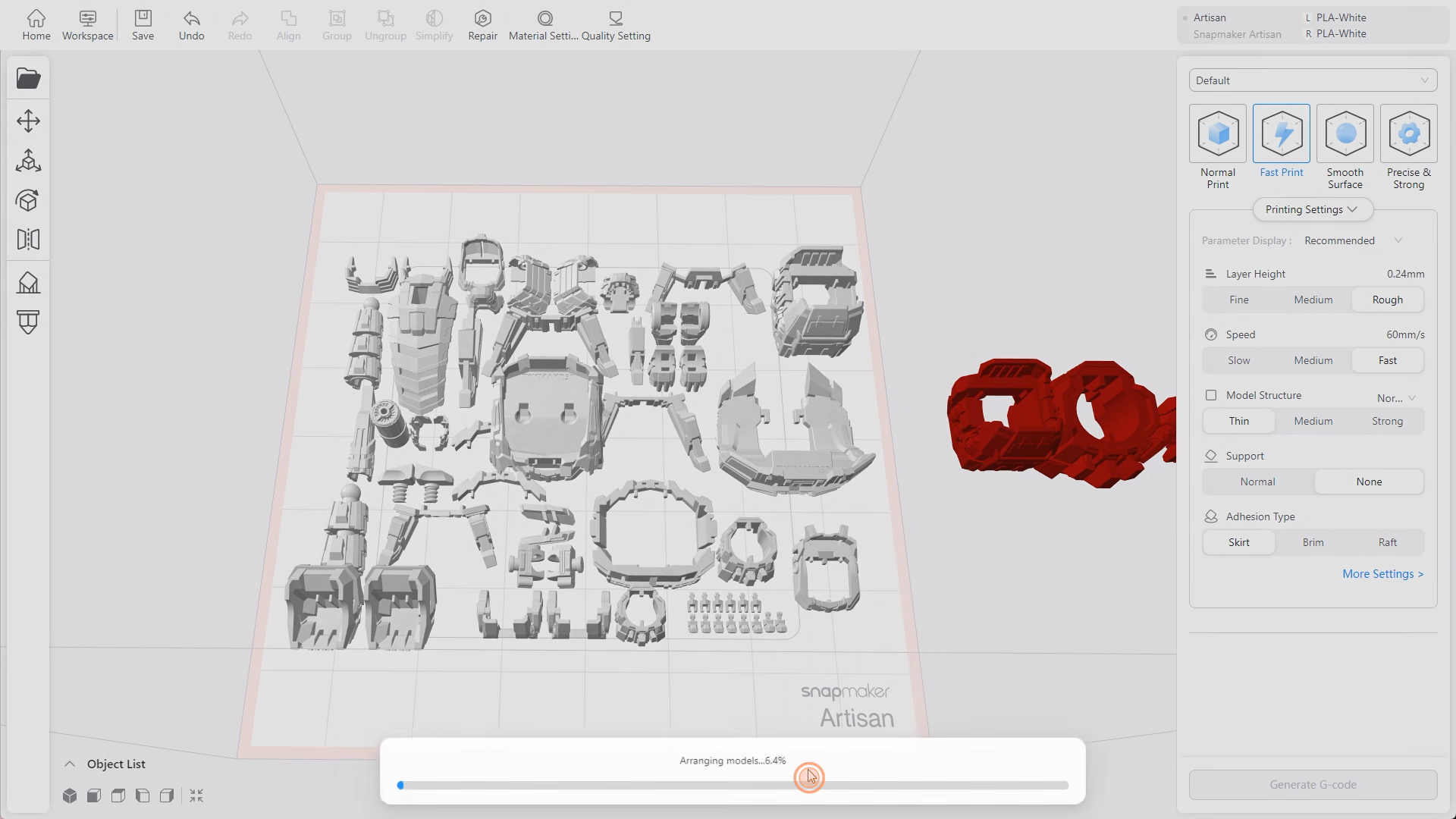
Bed Preparation and Filament Tips
To avoid adhesion issues, choose a glass build plate or use a build surface such as PEI and Painter’s Tape. BuildTak also helps, as it prevents prints from peeling or rolling off the surface when printing flexible filaments.
FDM vs. SLA vs. SLS on Flexible Material 3D Printing
FDM (fused deposition modeling) is the most easily available method nowadays for flexible material printing, where the use of TPU has dramatically improved print quality and durability. However, flexible filaments are not necessarily limited to FDM printing. Flexible filaments such as TPU can also be printed using SLA and SLS machines.
SLA or resin-based 3D printing creates parts with a slightly softer, more rubber-like finish. However, SLA resin must be flexible enough to avoid cracking.
SLS 3D printing also works with flexible materials such as TPU powder, which delivers excellent elasticity and rebound.
Final Thought
So, while you can't 3D print rubber, flexible filaments are a practical alternative. These materials open up new possibilities for creating flexible, durable, and high-performance 3D-printed parts, perfect for applications that demand elasticity, impact resistance, and longevity.