Snapmaker Artisan | The R&D Story Behind Artisan
For us, Artisan stands for an attitude of exquisite workmanship. To be an Artisan, one has to have the wildest ideas. To be an Artisan, one also has to be down to earth.
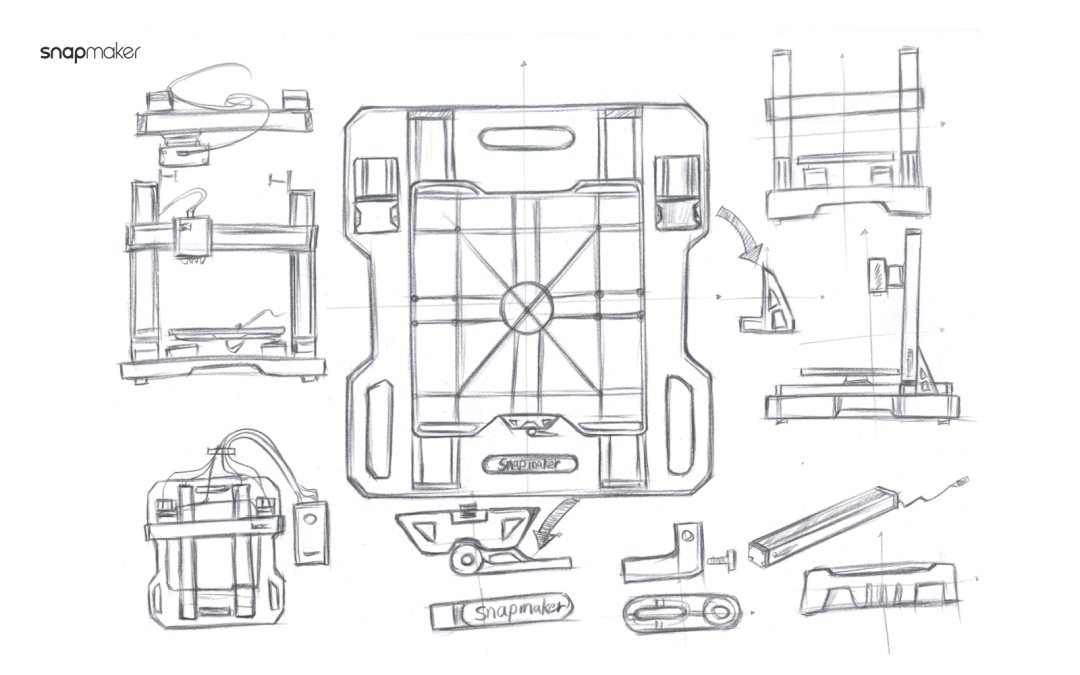
Hi makers,
Glad to e-meet you again. We hope you have caught up on the previous articles in our Snapmaker Artisan series. In Episode 6, we will reveal the story behind Artisan. Read on to find out more!
We made our debut on Kickstarter five years ago with Snapmaker Original 3-in-1 3D printer. We innovatively integrated three fabrication methods—3D Printing, Laser Engraving and Cutting, and CNC Carving into the body of one machine. With Snapmaker, you don't have to learn the know-how of machines for various fabrication types. It makes you excel in different fabrication scenarios and save your room space to a great extent. Over these years, we have witnessed so many users deeply love and benefit from the design of 3-in-1. In 2019, Snapmaker 2.0 was honored with the CES 2020 Innovation Awards. This year, Snapmaker won the International IF Design Award 2022. Among over 10000 entries from 49 countries, the Snapmaker 2.0 stands out in differentiation, function, and idea for its sleek all-metal modular design. Though Snapmaker 2.0 has enjoyed popularity among users, we have also recognized the need for better performance of each module, even higher quality, and a more user-friendly experience. Therefore, about two years ago, we started to plan on a product that can redefine the capability of a 3-in-1 3D printer. And we brought Artisan to the table—the strongest 3-in-1 3D printer in Snapmaker history.

We have met not a few challenges during the R&D of Artisan. One of them is developing the Dual Extrusion 3D Printing Module. In Episode 2, we have shown you the present design of our dual extruders. Behind the scenes, there were several iterations prior to the final version. Several months earlier, right before we moved on to the pilot run phase, we made the tough decision to change the design of the dual extruders. Under the former design, the dual extruders were heavier and larger. The switching between extruders was time-consuming and troublesome-the two extruders needed to be mechanically lifted, and hit either end to complete the switching. Also, it would generate more noises while in operation. We were not satisfied with this iteration. We could not accept a design that we didn’t like, let alone our users. To ensure product quality, we had to prolong the product development of the dual extruders. In our next try, the ultimate goal was to achieve efficiency in switching and calibration accuracy in a compact body. Therefore, the extruders were re-designed to be automatically lifted by the lead screw stepper motor, which enhances the swapping efficiency and eliminates the noise caused by mechanical lifting while resulting in a 30% decrease in size. We were able to control the weight of the dual extruders within 1KG, which can help minimize the influence of inertia in operation. We also added planetary reducers to ensure high-speed extrusion. Ultimately, we came up with a much better solution with optimized inner structure and improved functionality.
Delivering a product is a process of making a series of tough decisions. In the case of Artisan, we strived to solve three major conundrums. First, when we maxed out the capability of Artisan, we also had to ensure it remains a consumer 3D printer. As the size of the machine increases, the weight and the accompanying amount of machining go up exponentially. To decide what size Artisan should be in, we have done a series of thorough research. We went to IKEA to research common dimensions and load capacities of home desks. And finally, we pinned down the work area of Artisan on 400 mm × 400 mm × 400 mm. It is a size that would benefit small businesses and large-format prototyping. You can increase your production efficiency with this huge workspace and make large things like transportation or architecture models in one piece or print objects in batches. Moreover, we also take care of your need for printing models in small sizes by introducing Zone-heated Bed into Artisan. (See Episode 3)

Second, there is a trade-off between optimizing a single function and achieving the right balance among the three functions. In Artisan, the rigidity of the machine is determined by the requirements of CNC machining. The speed limit is determined by 3D printing, while the safety level depends on the laser function. By integrating three functions in one 3D printer, we did not lower our expectations for a single toolhead; instead, we made the performance of each toolhead as competitive as major alternatives in the market. Compared with Snapmaker 2.0, Artisan is fully improved in printing speed, precision, filament compatibility, and accessibility. The 10W Laser Module is equipped with the most cutting-edge laser beam splitters, leaping from 5W to 10W. The 200W CNC module is designed to meet the need for precision machining of hardwood like beech and walnut, jade, and other hard materials. Compared to Snapmaker 2.0, the 200W CNC module of Artisan has increased by 300% in power and 50% in max spindle speed.
Third, we had to align the product design with consumer needs while trying to downplay some unwanted impacts brought by adopting industrial-grade transmission technology. Linear rail is widely applied in industrial sectors such as industrial robots and transportation equipment. However, to fit linear rail in Artisan, we had to find a way to make it more compact and visually appealing. Specifically, steel guiderails made by CNC grinding at micron level are embedded in Artisan's linear modules. This innovation makes achieving micron-level accuracy possible while keeping the linear module relatively compact. Due to this upgrade, the repeatability accuracy of Artisan now measures ± 0.05 mm, whereas this spec is ± 0.08 mm in Snapmaker 2.0. To ensure better quality assurance, we build our own production line to mass produce the Next-Gen Linear Modules. Being the first manufacturer to use embedded steel-guiderail Linear Module in the consumer 3D printer industry, Snapmaker delivers this industrial technology to individual makers worldwide. We also thoughtfully designed the appearance of Artisan to align it with consumer product aesthetics. For example, we used the rounded corner in the design of the base plate and hollowed out some parts to give it a lighter look.
The development of Artisan is centered on two goals: lower the barrier to desktop fabrication and optimize the user experience. Working towards the first goal, we introduce the quick-swap mechanism in the hope that it can increase the swapping efficiency and let our users fully utilize the three toolheads in daily creation. On top of the 60s Quick-swap design, we will also release Luban 4.4.0, which will be more intuitive and let you prep for the fabrication process at ease.
To achieve the second goal of optimizing user experience, we provide much better fabrication quality, faster CNC machining and Laser Engraving and Cutting, and a larger work area in Artisan. With our new Laser Module, you no longer need to measure the thickness of your material manually; instead, the module will calculate it for you and adjust itself in Z orientation accordingly so that the focal point falls right on the material surface. In terms of firmware and software, the side navigation menu on the ultra-wide 7″ touchscreen enhances ease of navigation and truly streamlines your workflow. You can now preview the G-code files and check on the working status through live display on the new touchscreen.

In the near future, we will introduce Filament Dryer into the product line. Filament Dryer will be a good companion to your 3D printer. Filaments of different properties require proper storage temperature and humidity to function well. With the new Dual Extrusion 3D Printing Module, you can play with a wider range of materials, which makes a Filament Dryer more in need than ever.
Some of you might be curious about why we named our latest generation of 3-in-1 3D printer as Artisan. Well, it just came down to this name naturally. For us, Artisan stands for an attitude of exquisite workmanship. To be an Artisan, one has to have the wildest ideas. To be an Artisan, one also has to be down to earth. In the Snapmaker team, we encourage constant innovation that can contribute to a good product. We put considerable emphasis on R&D and treat every component of our product with attention to detail. Snapmaker's mission and vision is to enable everyone to create freely in the real world. We are now fulfilling this mission by introducing Artisan—a new generation of 3-in-1 3D printer to makers worldwide. You can realize three major fabrication methods with just one machine, create whatever comes to your mind. We believe our users value the ability to "make" as much as we do. We believe Artisan can be a versatile helper by your side and make you an Artisan of our time.
You can now get an Artisan at $2,949 (Enclosure Included) with Free Shipping. Preorder now!