Snapmaker Artisan | Quick-Swap Design, Large Work Area & More
Four great features contribute to ease of use, high performance, and high quality of Artisan.
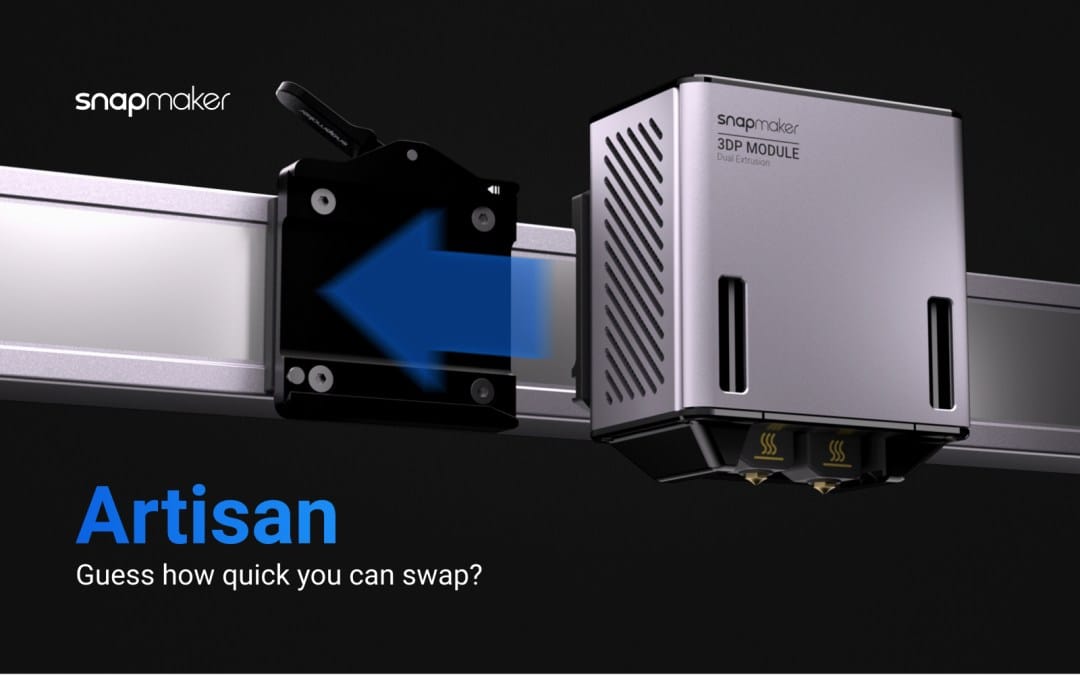
Hi makers,
Starting off with Next-Gen Linear Modules and three toolheads, the “Snapmaker Artisan” series now arrives at the third episode. In this article, you will get to know four great features that contribute to ease of use, high performance, and high quality of Artisan.
Seriously, No More Screws.
Easy to use is one of the key principles in product design. We make every endeavor to make your user experience as straightforward as possible. The tedious process of screwing and unscrewing is a common complaint in our community. To solve this problem, a quick-swap design is the way to go. In Artisan, quick-swap platforms and toolheads let you shift among three functions in one minute, making it super convenient to install and uninstall.
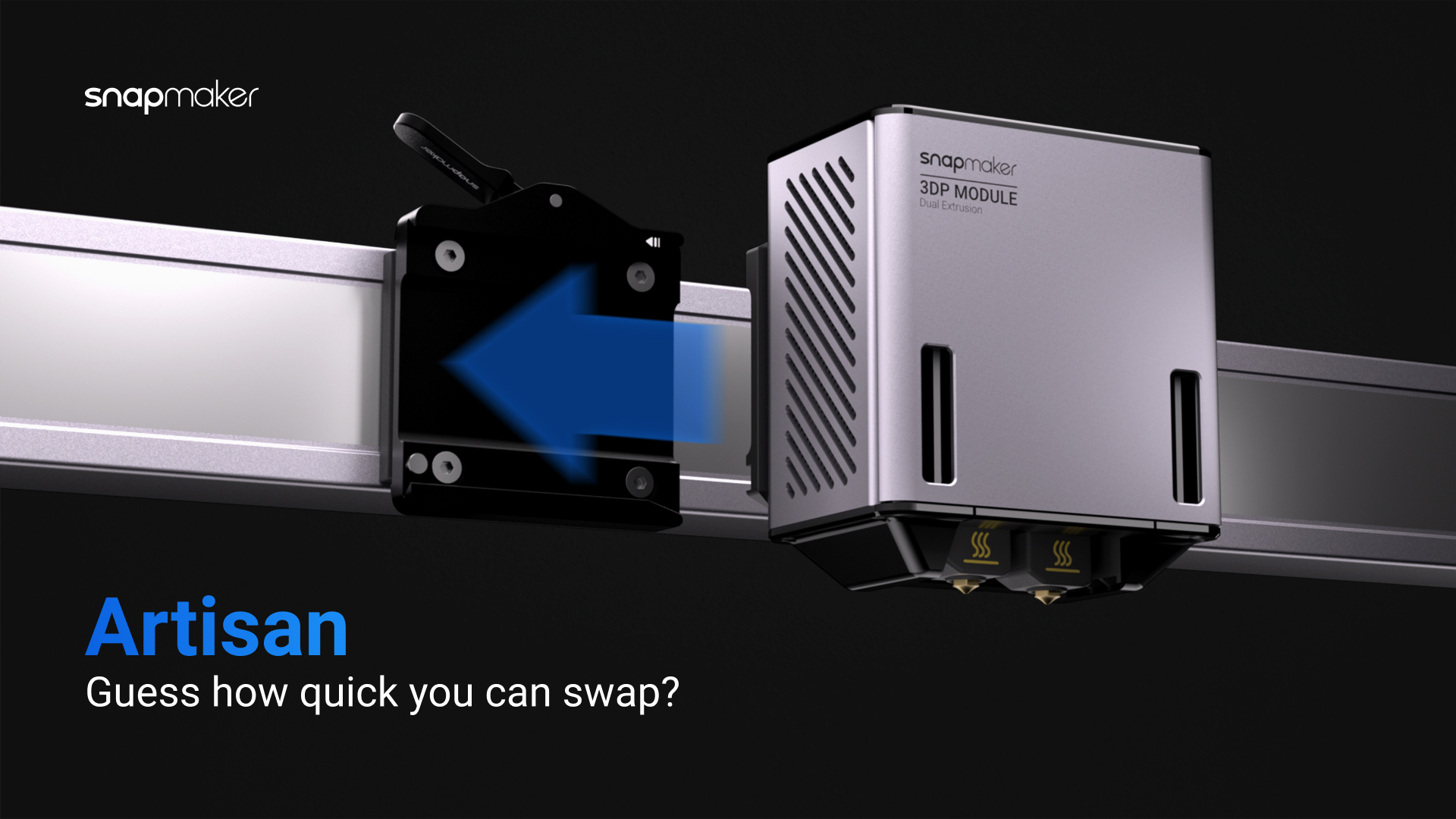
400 mm × 400 mm × 400 mm Work Area.
Many people love the large work area of Snapmaker 2.0. For Artisan, we level up the space for you to realize even bigger ideas. It allows you to make large things like transportation or architecture models in one piece. If you are a small business owner, you are able to max out the large work area to print products in batches!
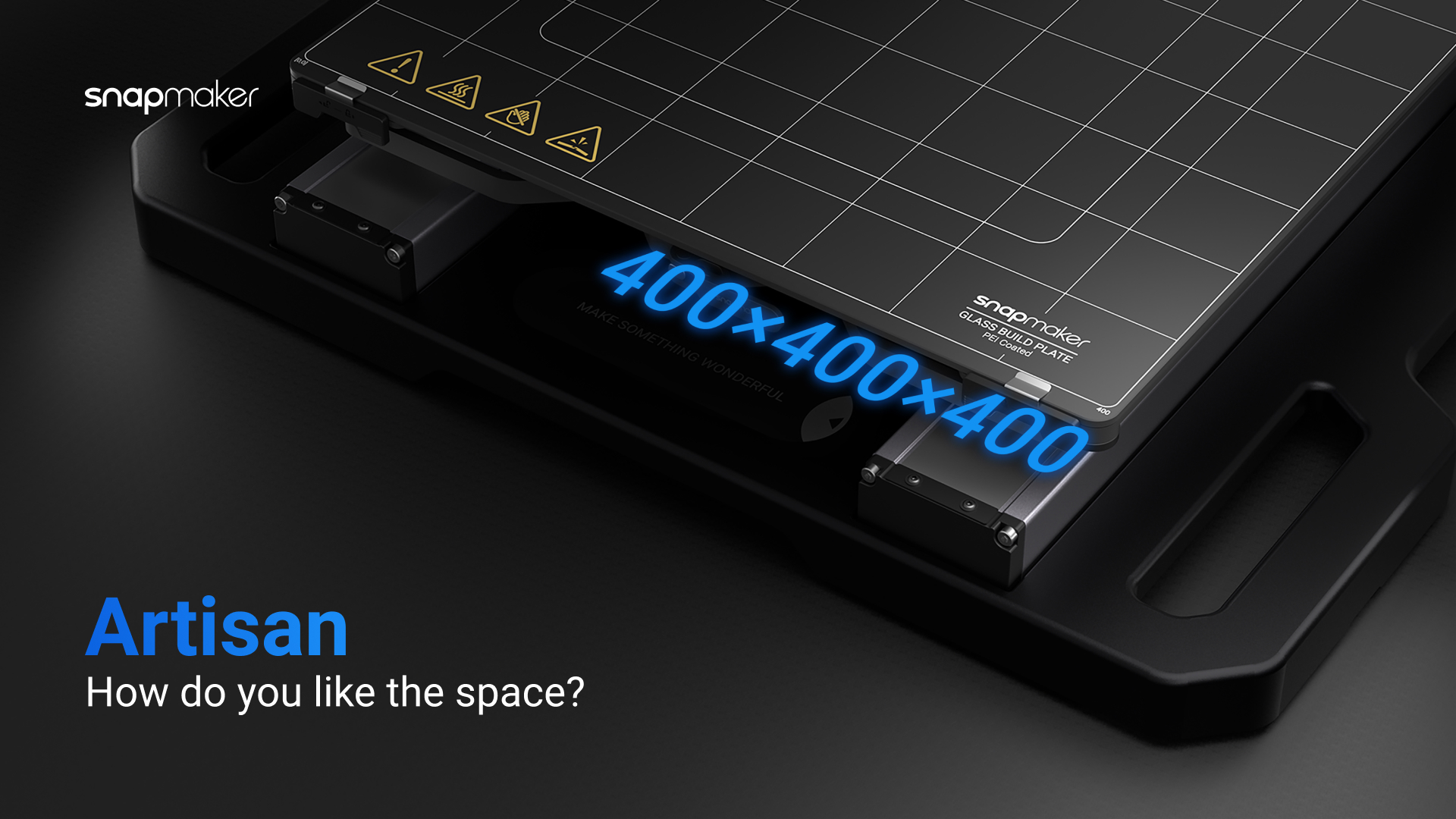
With 10W Laser Module and 200W CNC Module, the work area is up to 400 mm × 400 mm × 400 mm. With Dual Extrusion 3D printing Module, the maximum build volume is 400 mm × 400 mm × 400 mm when printing with only the right nozzle, 375 mm × 400 mm × 400 mm when printing with only the left nozzle.
Save Time and Power with Zone-heated Bed.
Even though we offer a huge bed at your disposal, we still take care of your need for printing stuff in relatively small sizes. That’s why we introduced Zone-heated Bed into Artisan. In the middle of Artisan's heated bed lies a 260 × 260 mm high-temperature zone (aka inner zone) that can reach 110°C, whereas the maximum temperature of the outer zone is 80°C. While your model is placed within the inner zone, which heats up to 60°C in only 2–3 minutes, the outer zone won't be heated, saving time and energy. What’s more, the heated bed is usually susceptible to warping as the temperature goes up; yet, the one-piece die-cast bed fixing frame at the back of the heated bed helps guarantee the flatness of the bed.
All-metal. Next Level.
High quality as always. Artisan inherits Snapmaker’s signature all-metal design. It also comes with an upgraded one-piece die-cast base plate in a larger size, which is as steady as a rock even during high-speed CNC machining.
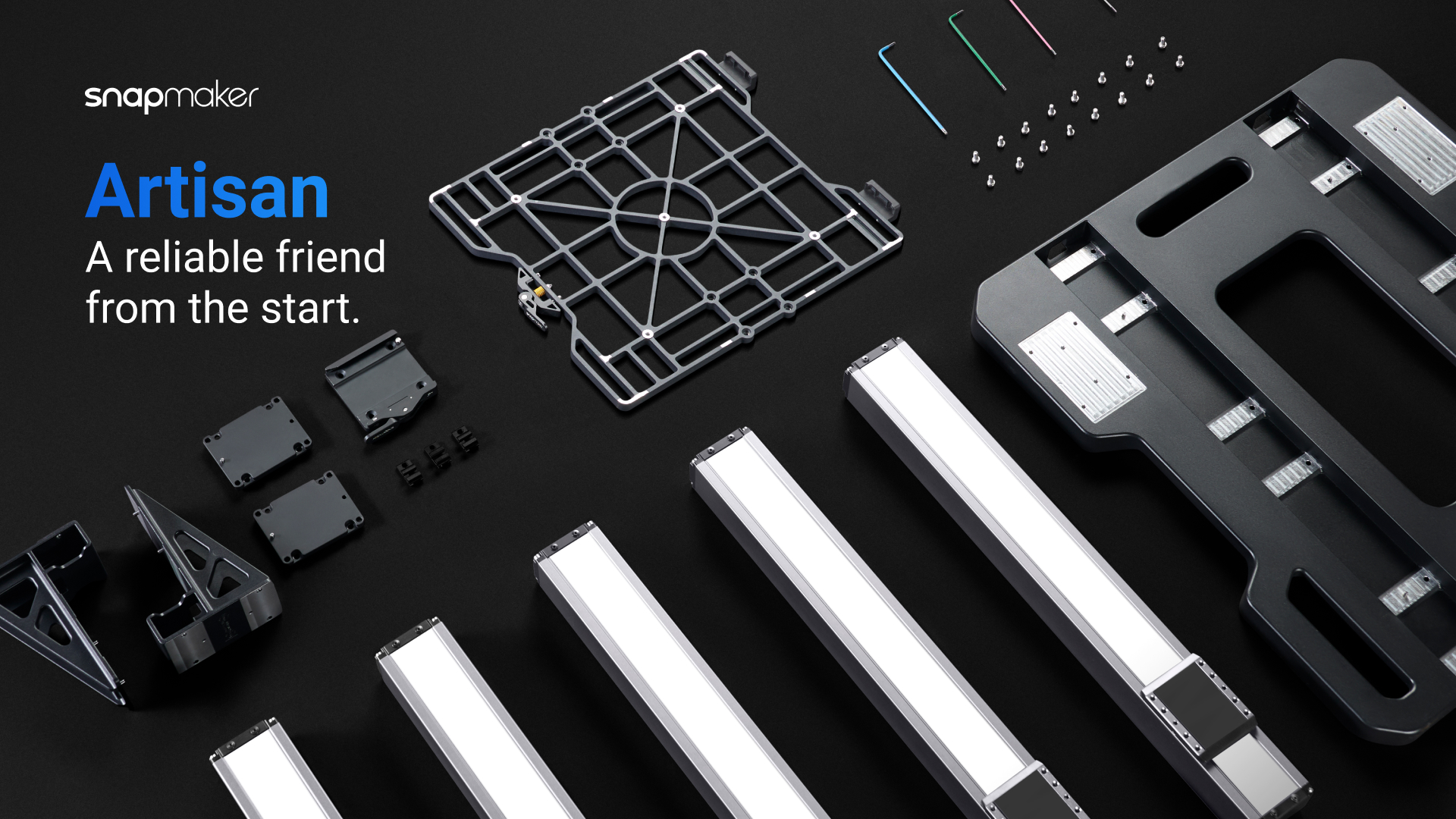
We hope you like these four features as much as we do!
Stay with us!