Snapmaker Artisan | Next-Gen Linear Modules
Turn Your Desktop Into a Workshop

Hi makers,
It's been a long and arduous journey, and we are finally able to tell you the moment has arrived—the moment to unveil a new generation of 3-in-1 3D printer in front of you. After Snapmaker 2.0, we spent 516 days crafting a brand new product that aims to push the limit of what a 3-in-1 3D printer can do and named it Artisan. It can meet the needs of different fabrication scenarios and truly turn your desktop into a workshop. The high quality and high performance that Artisan has to offer can unleash your creativity and make you an Artisan of our time. Snapmaker Artisan is not simply an upgrade based on Snapmaker 2.0 but sets a new standard for 3-in-1 3D printers.
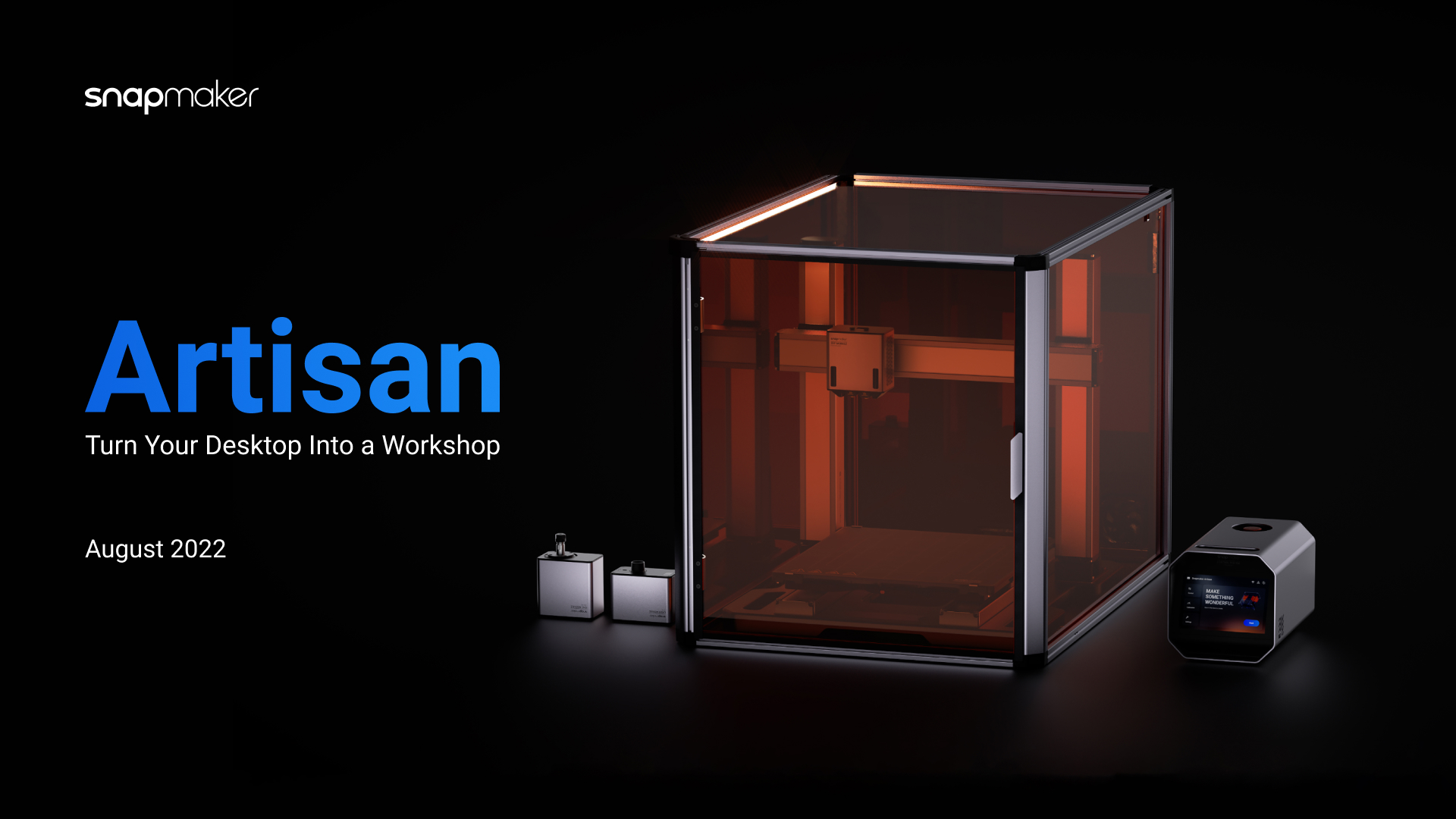
In July, we are going to publish a series of articles to unpack every aspect of Snapmaker Artisan. You will read about some amazing features that we really want to yell out, R&D stories of Artisan, considerations behind the product design, and how we've always treasured feedback from our community. We will traverse you through an exhilarating product journey!
Featuring the Linear Module, this article is the first of the "Snapmaker Artisan" series. The motion system is the backbone of any given fabrication machine. The performance of the motion system is closely related to the machine's overall performance. Therefore, in the introductory episode, we would like to walk you through Next-Gen Linear Modules in Snapmaker Artisan.
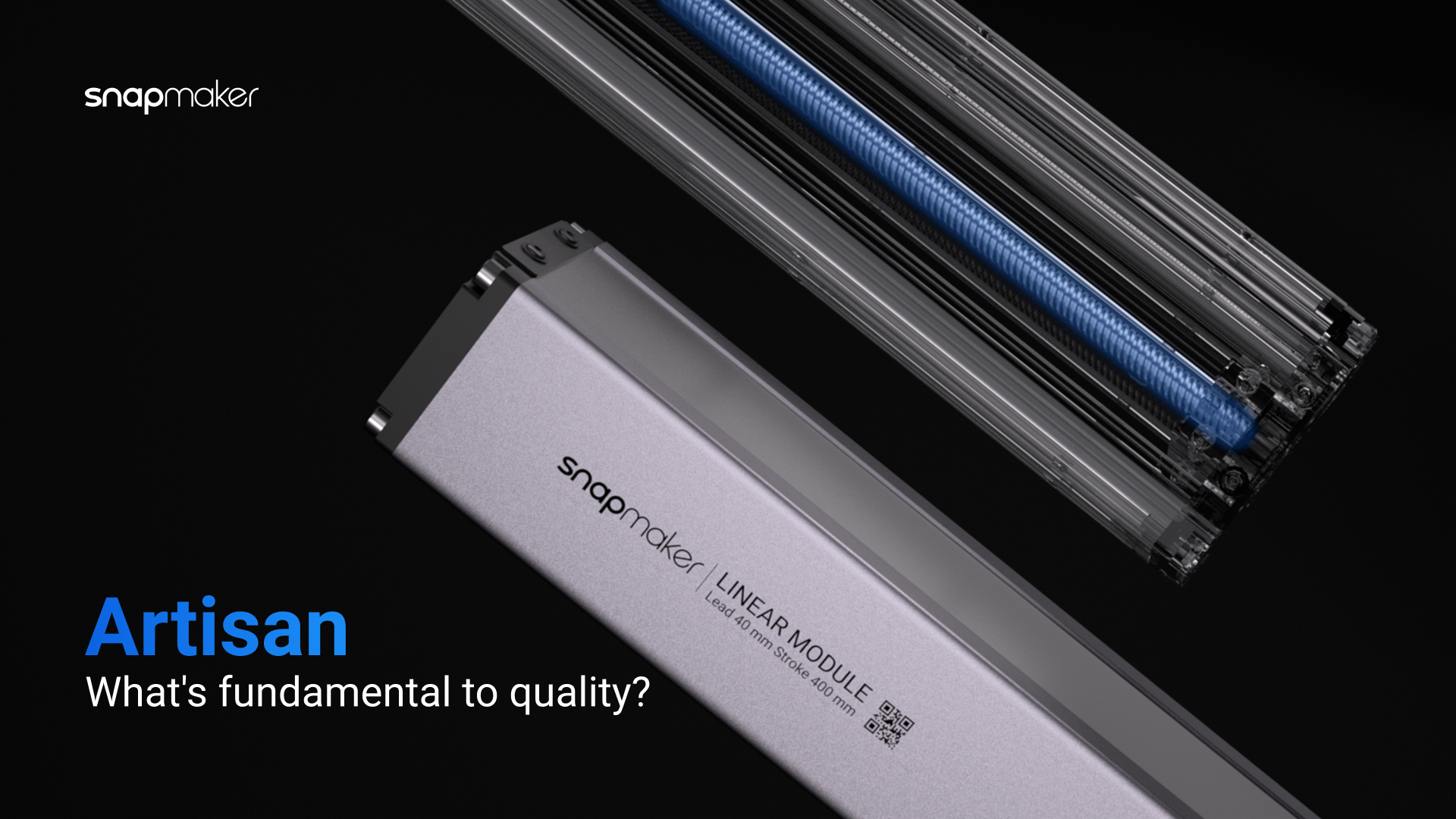
Next-Gen Linear Modules
Widely applied in industrial sectors such as industrial robots and transportation equipment, linear rail is a device that ensures a piece of equipment strictly follows the desired path in both the vertical and horizontal dimensions. In the case of a 3D printer like Snapmaker, that equipment would be toolheads of 3D Printing, Laser Engraving and Cutting, and CNC Carving.
Let's go inside our Next-Gen Linear Module to see what makes achieving micron-level accuracy possible. You might wonder why the accuracy of Linear Modules matters. To give you a bit of basics, it's all about positioning the toolheads in the right place, which depends heavily on two essential components of a linear guide-bearings and the drive unit. In Artisan, we improve both components to optimize the performance of our Linear Modules. First, let's talk about the bearings. Previously in Snapmaker 2.0, the bearings are a combination of linear rods and pulleys. The application of linear rods is common to see in many 3D printers available on the market. However, linear rods are less capable of providing a smoother motion with higher precision. Linear rails, on the other hand, allow for a more rigid motion mechanism. It is less susceptible to vibration and thus also reduces printing problems like ringing.
Instead of the regular linear rails, we introduce industrial-grade transmission technology to desktop fabrication—steel guiderails made by CNC grinding at micron level are embedded in Artisan's linear modules.
As with the drive unit, we applied Gates high-end synchronous belts in the X and Y axes to optimize the lead, which boosts the power transmission efficiency while maintaining high accuracy and low noise level. Compared to the transport lead screw used in AT models, the leads of the X and Y axes of Artisan were increased from 20mm to 40mm.
Taken together, the improvements in bearings and drive unit take the performance of our Linear Modules to the next level. Both the straightness errors and flatness errors now measure within 0.04mm, whereas the positioning accuracy measures within 0.1mm. And how is this reflected in the performance of 3D printing and CNC carving? In a nutshell, Snapmaker Artisan can operate at a higher speed and achieve higher printing quality simultaneously by taking advantage of superior Linear Modules. If you speed things up, it can achieve ±0.1 mm dimensional accuracy at a high speed of 150 mm/s to 180 mm/s[1]. The new Linear Modules also secure steadiness for CNC machining.
To recap, all these lead to a significant rise in precision, rigidity, and durability, bringing you a fast, accurate, and steady-making experience. We are proud to say that Snapmaker is the first manufacturer to use embedded steel-guiderail Linear Module in the consumer 3D printer industry. We bring it to the table of consumer printers and deliver this industrial technology to individual makers worldwide.
So much for the first episode. Drop your thoughts and comments below. We’d love to hear! The next episode will feature the three new toolheads of Snapmaker Artisan. Stay tuned!
[1] The test result was obtained by printing a 100 mm × 100 mm × 100 mm cube with PLA filament, and using 0.4 mm nozzle. Dimensional accuracy may vary depending on the testing conditions and product iteration, and is for reference only.