Another new feature added! Upgraded design of the Snapmaker 2.0 3D printing module & test progress
Today, we bring you the upgraded design of the 3D Printing Module and news on the test progress of the initial trial run.
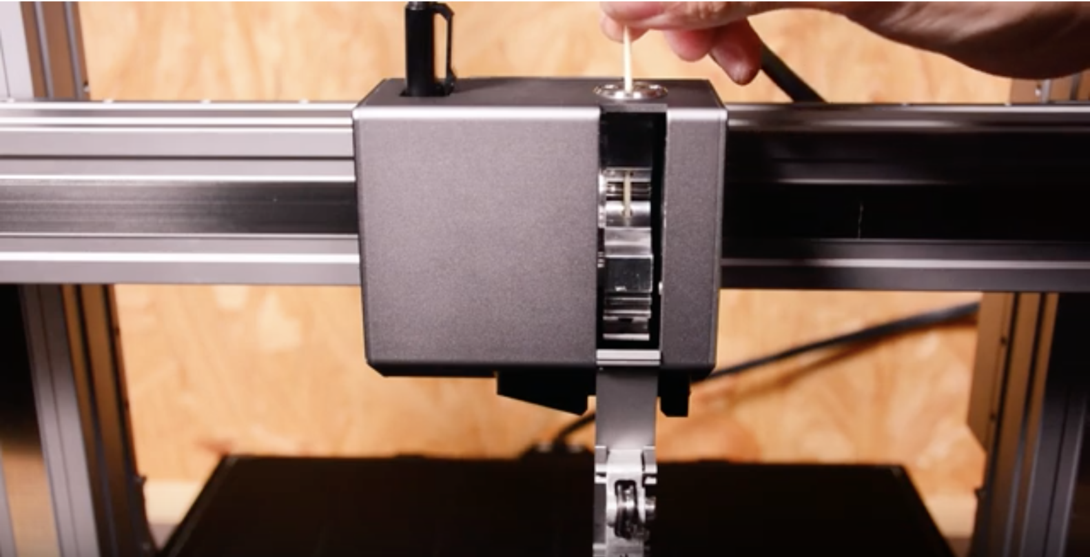
Today, we bring you the upgraded design of the 3D Printing Module and news on the test progress of the initial trial run.
Sneak peek at the upgraded design of the 3D printing module
Further improved the success rate and user experience of loading filament
From the feedback of our original model’s users, we found that it’s a little bit hard to push the physical button to load filament, and there remained a small possibility of failing to load filament in the right position which results in the problem of filament breaking inside the 3D Printing Module. To improve the success rate and user experience of loading filament, we developed an auto-loading-filament feature in Snapmaker 2.0. Users can easily load or unload filament using the touchscreen without pushing hard on the physical button on the 3D Printing Module.
In addition, we’ve kept working on the improvement of the manual loading method as well. Now you are one of the first to have a look at the upgraded design of our 3D Printing Module. Simply switch the button on the module to open the cover of the extruder, and then you can insert filament directly into the hole for loading filament. This process is very intuitive and you can spot a mistake immediately if there is something wrong. It also allows you to clean the extruder drive gear conveniently.
The video below shows the improved manual loading method and the newly added quick-release feature.
Added quick-release feature for quicker troubleshooting and maintenance
Generally, after printing for some time, the nozzle and hot end may get worn, which requires replacement of a new nozzle or hot end in some troubleshooting cases. For our original model, replacing a hot end is a little bit tricky: you need to remove the side cover of the module and then remove the fan to disassemble the hot end. We’ve been thinking of a better design. Now we are pleased to announce that we’ve made it. The Snapmaker 2.0 3D Printing Module will be upgraded with the quick-release feature. This new design saves you time in replacing the hot end. It simplifies the steps to switching a button, removing the screw on the hot end, and then taking out the hot end.
The latest progress of modules testing in the initial trial run
Over the past month, we’ve completed around 80% of testing on average for each module. Most test results meet our standards. A few unexpected problems arose during the testing. To solve them, we have improved some of the assembly methods, conducted extra tests to figure out how to solve the problems, and communicated with suppliers to further fine tune the design of some components. We know that in testing, we can’t expect things always go the way we want and that the challenges we meet will be valuable and well worth the extra time, effort and money to make our products even better.
We’ve completed 3D printing tests on various materials including PLA, ABS, TPU, PETG, and PVA in different scenarios. These scenarios include filament loading/extruding/unloading and filament runout recovery. All of these materials passed our tests. We will complete all the tests in Modules Testing and move on to the next phase, Whole Machine Testing, by the end of this month. At that time, we will test more materials and use more test models, including Autodesk & Kickstarter Test Print.
Much love,
The Snapmaker Team