Bring 3D Printing Into Art and Design: An Interview With Content Creator Zi Hao Low
Recently, we had the chance to speak with the talented Content Creator and Product Designer Zi Hao Low from Singapore.
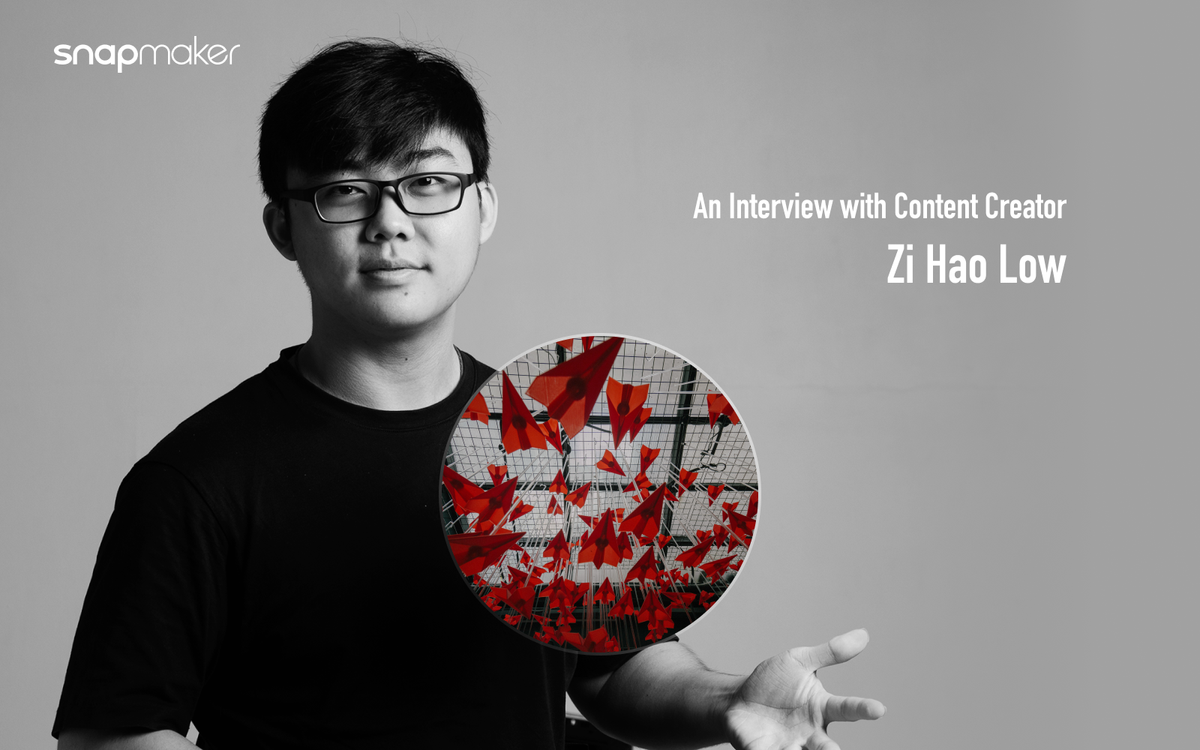
Recently, we had the chance to speak with the talented Content Creator and Product Designer Zi Hao Low from Singapore, who has been a Snapmaker 2.0 user for a year. In our conversation, he talked about how he started 3D printing and brought it to various commissioned projects, and shared his vision of integrating 3D printing into education and the future of desktop FDM 3D printers. Read on to learn more about him and his journey with 3D printing.
Who is Zi Hao Low?
As an undergraduate student pursuing a Bachelor of Fine Arts (Honors) at the School of Art, Design, and Media at Nanyang Technological University in Singapore, Zi Hao is dedicated to developing his artistic and design skills through his coursework and independent projects. He is currently focused on the study of product design. In addition to his academic pursuits, Zi Hao is also the founder of Para ( ) Studios and a content creator.
Zi Hao's personal belief is that the process of learning and exploring new mediums is an ongoing journey that is essential to personal growth. He recognizes that the more skills he acquires, the more possibilities he has for creating new and meaningful work. He also understands that a growth mindset, which allows him to be open to new ideas and perspectives, is crucial for identifying and seizing opportunities for further learning and development.
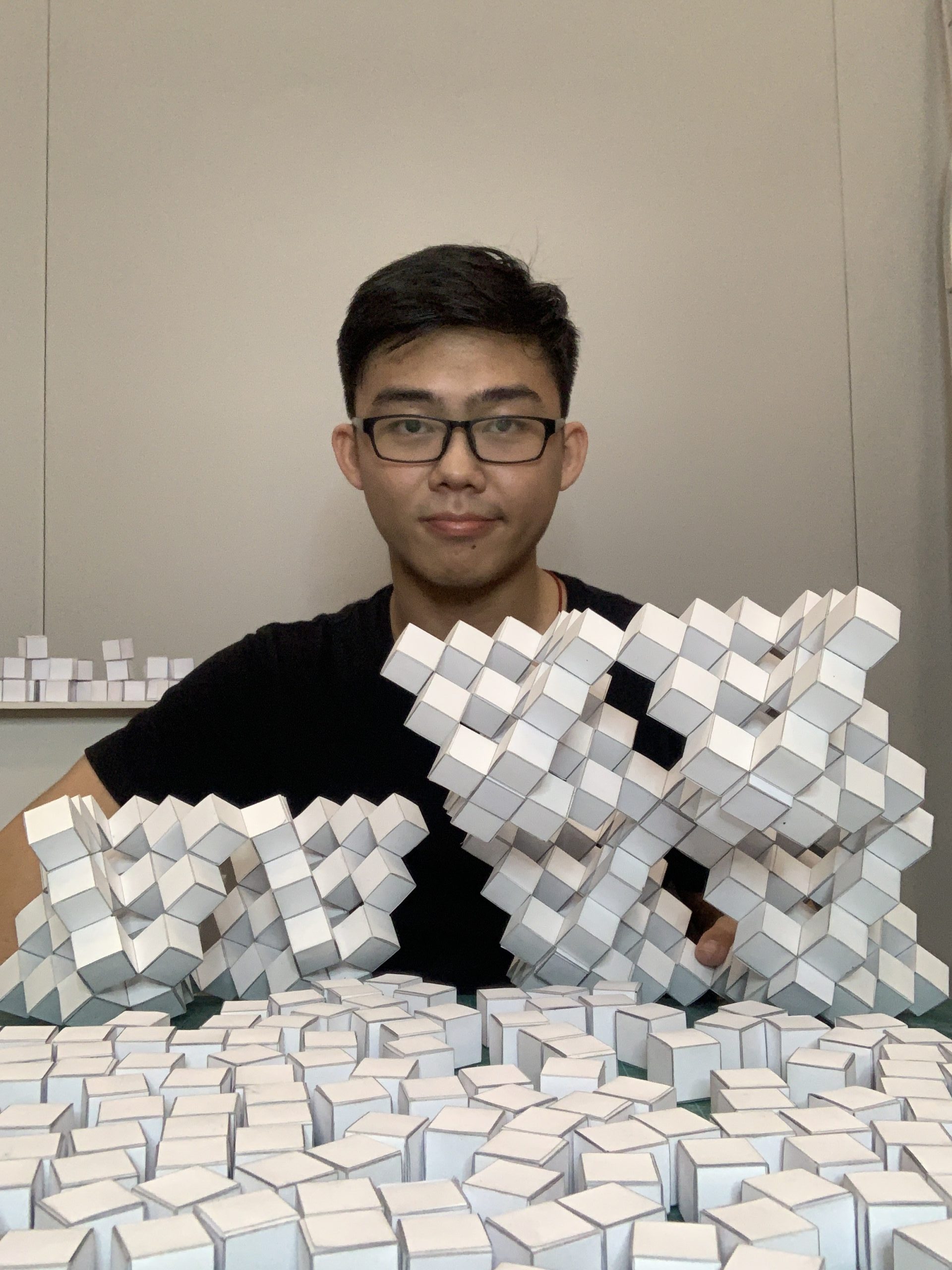
An Interview with Zi Hao
Snapmaker: When and how did you find your way to 3D printing?
Zi Hao: I started 3D printing approximately 2 years ago, in 2021, out of necessity. As a product designer, I quickly realized that rapid prototyping was a critical step in creating design iterations and enhancing the overall quality of my projects. However, my passion for 3D printing didn't end with my work. In my free time, I enjoy tinkering around and printing random objects, both as a hobby and as a way to hone my skills in using a 3D printer. Overall, 3D printing has become an essential tool for me as a designer and a fun pastime that allows me to explore my creativity.
SM: How’s your experience with Snapmaker 3D printer? What do you love about Snapmaker 3D printers? What can be improved?
ZH: I have been using the Snapmaker 2.0 A350T for almost a year now, and I must say, it is one of the most dependable 3D printers I have ever worked with. As an owner of a printing farm consisting of about 16 printers from different brands, I have tested multiple consumer-grade desktop 3D printers, and the A350T stands out for its consistency.
What sets the A350T apart is its unwavering reliability. I once had to run all my printers 24/7 for two straight weeks to complete a commercial project on time. While some of my smaller printers gave me trouble, the A350T kept running smoothly without any issues. I only had to switch the nozzle once every 1-2 months, and it was good to go again. The only downside I have noticed is the sound produced by the A350T. Although it's not a major issue, it's something that could be improved upon.
SM: How do you think Snapmaker 3-in-1 3D Printer can help you with your art and design? Do you also use laser and CNC functions for your projects?
ZH: I have found 3D printing to be an incredibly helpful tool in my work. While it is traditionally used for prototyping, I am working to promote it as a viable finishing product. Additionally, I have found the CNC and Laser Cutting modules to be useful in my projects. I use the Laser Cutting tool occasionally for simpler models that don't require 3D printing, and while the CNC module is effective, the clean-up process makes it more time-consuming and requires more effort for me to use.
SM: You often have multi-disciplinary collaborations with different companies and industries. What kind of role did 3D printing play in the realization of these commissioned projects?
ZH: Fine details are also achievable with the A350T, allowing for a high level of accuracy in the final product. As a professional who frequently undertakes large-scale projects with various clients, I strive to create bespoke solutions tailored to their specific requirements. One of the significant advantages of utilizing 3D printing technology is the ability to rapidly produce custom designs. Recently, I had the pleasure of working with a newly opened bar in Singapore, where I utilized the Snapmaker 2.0 A350T to create 3D-printed planes for a ceiling installation.


A 3D printed ceiling installation at The Kongsee, an open bar in Singapore
This not only impressed my client but also allowed them to physically experience the prototypes with a range of options available, including scaling, textures, and colors. The A350T proved to be an excellent choice for this project, delivering quality-looking prints with exceptional precision and detail. The ability to bring a client's vision to life is something that is highly valued in my profession, and 3D printing makes this entire process of project management much more efficient and effective.
SM: What materials do you regularly work with? We know that you are very into paper craft which has a different medium compared to 3D printing. Does 3D printing open up some new possibilities for your art and design?
ZH: As a designer, I enjoy working with a wide range of materials, and paper is one that particularly fascinates me. Like 3D printing, paper is incredibly versatile and has many potential use cases. I love exploring origami and parametric ideas, and often find ways to incorporate elements of both 3D printing and origami in my work.
As mentioned, I was commissioned to create an origami plane ceiling installation. While I initially considered using paper as the material, my concern was that the planes might not be durable enough for long-term use. This led me to think about alternative materials, and 3D printing immediately came to mind. Unlike paper, 3D printing offers superior durability, can be quickly fabricated without any supports and is much easier to maintain over time.


A close-up of 3D-printed planes
After proposing this idea to my client, they were impressed with the potential of 3D printing and agreed to move forward with this approach. This project has opened up new opportunities and options for me as a designer, and I'm excited to continue exploring the intersection between 3D printing and traditional materials like paper in my future work.
SM: Could you talk more about your paper plane ceiling installation?
ZH: Creating the 3D-printed plane installation was a fascinating experience, especially since it was my first time working on a project of this magnitude. Unlike other installations, ceiling-mounted pieces present unique challenges as they involve public safety concerns when hanging overhead. After receiving client approval and providing quick renderings, I set to work fabricating 800 3D-printed planes, using the A350T to print not only the planes but also the brackets that were subsequently attached to each plane.
Snapmaker 2.0 A350T in action
One of the significant advantages of 3D printing was that I was able to print all 800 planes in a single week, thanks to the 16 printers in my print farm. While I faced some challenges with print quality inconsistency and print failures when using other printers, the planes printed with the A350T required no post-processing and had zero print failures.
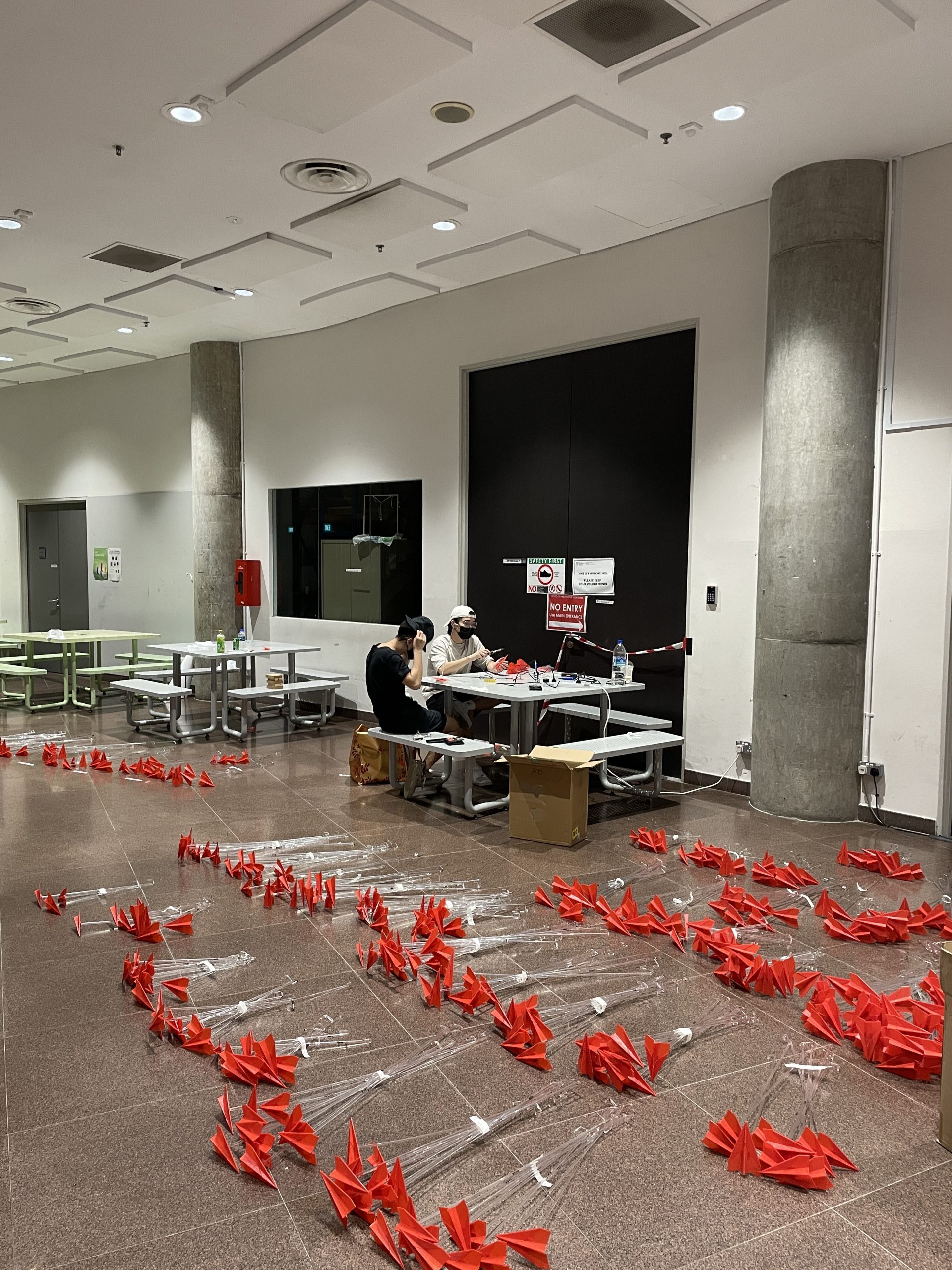
Installation was straightforward, as I designed the planes to be easily hooked onto the brackets. Despite the challenges associated with such a project, the overall experience was relatively smooth, and the end result was a satisfied client.
SM: We are also interested in your 3D-printed kinetic sculpture recently exhibited at the Singapore Chinese Cultural Center. Could you tell us more about this project? It seems to me that it’s part of your kinetic structure series.
ZH: Creating this kinetic 3D-printed sculpture for the 2023 Singapore Art Week exhibition was a thrilling experience. Standing at 1.1m tall, this sculpture was an adaptation of a kinetic piece I created the previous year. However, what made this exhibition particularly exciting was the opportunity to engage with the public and address their skepticism about 3D printing's role in art.

I relished the opportunity to explain my creative process and how I use 3D printing as a tool to bring my ideas to life. Ultimately, my workflow involves digitally designing the models using 3D software and then 3D printing the modules, which are then manually pieced together to create the final sculpture.
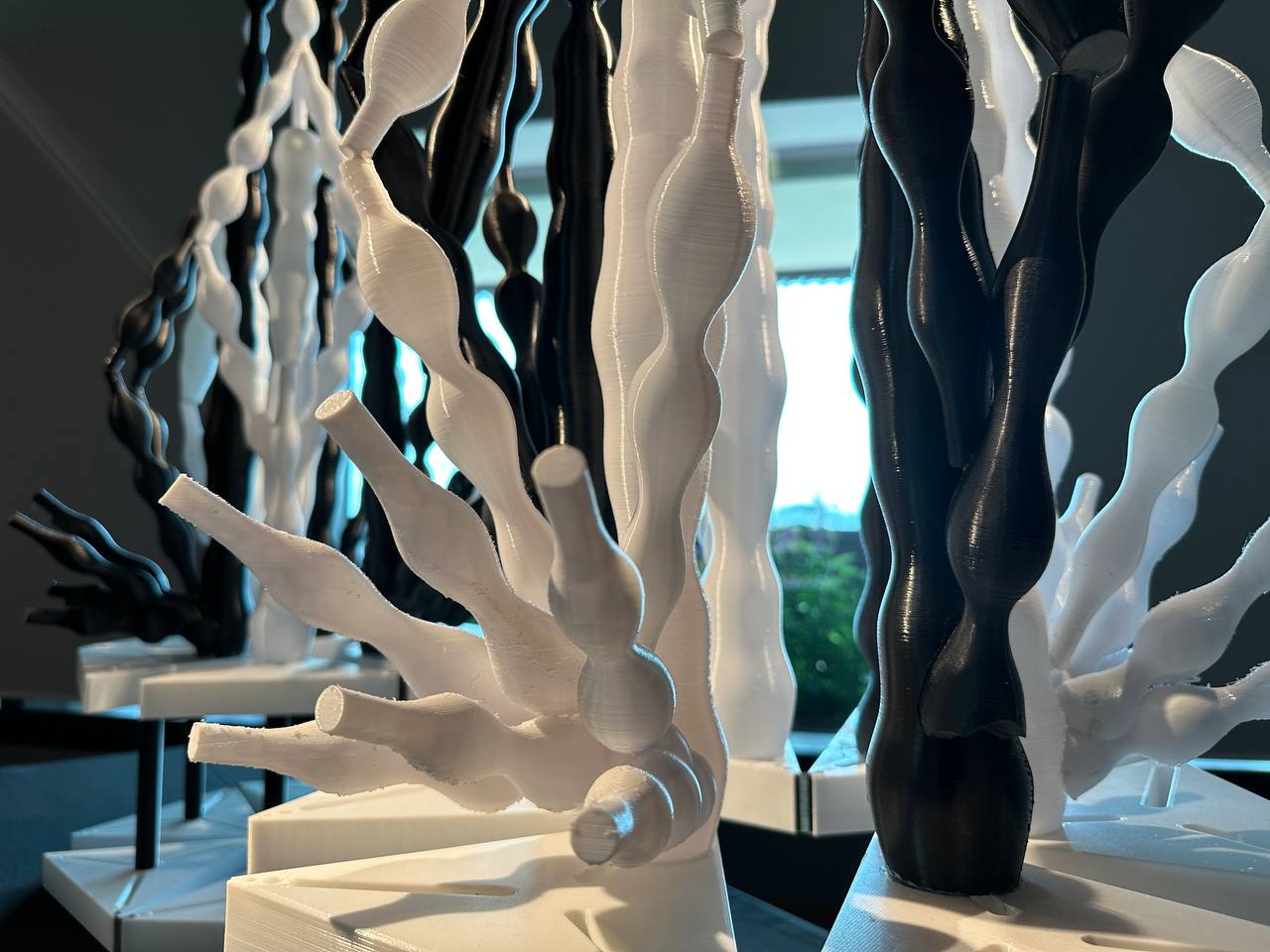
Through this exhibition, I was able to engage with the audience and explore the intersection of art and technology, demonstrating how 3D printing can be used as a creative medium, just like any other tool. The end result was a kinetic sculpture that challenged conventional notions of what constitutes art.
SM: We also noticed that you ran education workshops from time to time. In your opinion, how 3D printing will fit into future education? Why is it essential for students nowadays to have access to this emerging technology?
ZH: While I have conducted paper craft workshops for youths and adults, I have yet to organize a 3D printing workshop. However, I believe that there is enormous potential in conducting 3D printing workshops, particularly for the younger generation. By exposing children to this technology at an early age, we can inspire them to think creatively and explore the vast array of possibilities that 3D printing offers.
Over the years, entry-level 3D printers have improved significantly, making it easier for people to access and utilize this technology. In fact, I envision a future where 3D printers become as ubiquitous as 2D printers in our homes.
By introducing students to emerging technologies such as 3D printing, we can help to push the boundaries of what is possible and foster innovation that can positively impact society. Ultimately, these young minds will be the ones to continue pushing the limits of this technology, creating new applications, and driving further progress in this field.
SM: As a designer, do you have any expectations for the future of desktop FDM 3D printers?
ZH: In the future, FDM 3D printers should be designed to be as user-friendly as our everyday 2D photocopy printers, requiring only a few clicks to operate. Designers should not have to comprehend the technical intricacies of the printer components. As technology and artificial intelligence continue to advance at a rapid pace, I believe that FDM printers will become increasingly affordable and accessible to everyone. It is intriguing to consider how the intersection of these two fields will shape the future, and the possibilities that lie ahead are exciting!